Ndfeb hydrogen decrepitation.jpeg.
Seven methods of production have been summarized, starting with the conventional powder metallurgy route and ending by the Hydrogen Decrepitation (HD) route, as they are the most applicable routes in this field. The advantages and disadvantages of the reported routes were mentioned. In fact, the HD method was found to have the following ...
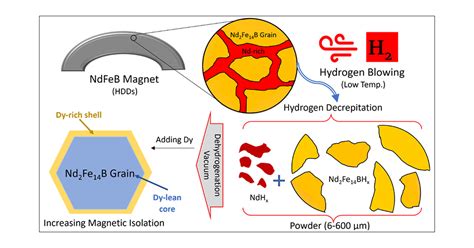
Sep 7, 2022 · We report investigations on the processing by Spark Plasma Sintering (SPS) of RE2Fe14B (RE = Nd, Pr…) powders obtained by hydrogen decrepitation of decommissioned magnets and the magnetic properties of the consolidated magnets. First experiments have been carried out with a commercial powder to make clear the mechanisms occurring during the powder densification. The magnetic properties of ... A combination of hydrogen decrepitation (HD) and jet milling (JM) has been used to produce powder for the processing of permanent magnets. The procedure has proved to be very successful for both Nd-Fe-B (Neomax) alloys and the ND-Dy-Fe-Nb-B high coercivity alloys. The magnets produced by the HD/JM process showed excellent coercivities when …At these elevated tempera- tures the decrepitation process proceeded rapidly and particles were ejected from the sample on all sides, V.A. Yartys et al. / Journal of Alloys and Compounds 239 (1996) 50-54 53 Fig. 2. Surface of a plate ejected from the [001 ] aligned sintered Nd16FeTaB8 magnet at the first stage of hydrogen decrepitation.Hydrogen absorption/adsorption properties of high coercivity NdDyFeCoNbCuB sintered magnets were determined. Hydrogenation kinetics were analyzed using both differential scanning calorimetry (DSC) and X-ray diffraction (XRD). Hydrogenation of the Nd-rich intergranular phase results in a rather broad and large peak …Sintered Nd-Fe-B magnets were subjected to the Hydrogen Decrepitation (HD) process at various temperatures in the range of 50-300°C, at two different pressures, 50 kPa and 200 kPa, followed by ...
Mar 1, 2019 · Fig. 1 shows the hydrogen decrepitation curves of Nd-Fe-B SC and SM at 288 K with different initial hydrogen pressure. Under the initial hydrogen pressure of 0.1–1 Mpa, the HD process composes of four stages of magnets surface activation, slow hydrogenation of Nd-rich grain boundary phase, quick hydrogenation of Nd 2 Fe 14 B main phase grains, and slow hydrogenation of inner part of the magnets.
Mar 14, 2016 · Hydrogen decrepitation (HD)/hydrogenation disproportionation desorption recombination (HDDR) is a process used in manufacturing REPM and carried out as pretreatment before green body sintering. During hydrogenation, the Nd-rich grain boundary phase in NdFeB magnets initially absorbs hydrogen forming Nd hydride: [ 49 ]. 99.5%. The strips were employed in hydrogen decrepitation (HD) into coarse fragile particles. These coarse particles were then sent into jet milling (JM) procedure under a N. 2. gas flow. The dry powder was compacted of 14 mm diameter and 15 mm height with the alignment made with the maximum 2 T magnetic field.
The decrepitation process and related changes in the sample temperature are analysed to explain the experimentally observed weight gain curve of a Nd–Fe–B sample due to hydrogen uptake. It is shown that the expansion of the specific surface resulting from decrepitation of the sample is the most important parameter controlling …Aug 4, 2022 · One of the most promising solutions with regards to extraction of end-of-life (EOL) magnets is to apply hydrogen decrepitation and to physically separate the Nd-Fe-B as a demagnetized... Hydrogen absorption/adsorption properties of high coercivity NdDyFeCoNbCuB sintered magnets were determined. Hydrogenation kinetics were analyzed using both differential scanning calorimetry (DSC) and X-ray diffraction (XRD). Hydrogenation of the Nd-rich intergranular phase results in a rather broad and large peak …May 8, 2023 · An effective and complete processing route for the recycling of sintered Nd-Fe-B scrap magnets was proposed. Sintered Nd-Fe-B magnets were subjected to the Hydrogen Decrepitation (HD) process at ...
Jul 14, 2000 · The decrepitation process and related changes in the sample temperature are analysed to explain the experimentally observed weight gain curve of a Nd–Fe–B sample due to hydrogen uptake. It is shown that the expansion of the specific surface resulting from decrepitation of the sample is the most important parameter controlling the hydrogen ...
The scrap sintered Nd–Fe–B magnets were recycled as the raw materials for bonded magnets using the hydrogen decrepitation (HD) process. The HD powders have the lowest oxygen and hydrogen content by hydrogenation at 150 °C with 1 bar H2 pressure and dehydrogenation at 600 °C. The powders with the largest particle size (>380 μm) …
A combination of hydrogen decrepitation (HD) and jet milling (JM) has been used to produce powder for the processing of permanent magnets. The procedure has proved to be very successful for both Nd-Fe-B (Neomax) alloys and the ND-Dy-Fe-Nb-B high coercivity alloys. The magnets produced by the HD/JM process showed excellent coercivities when …Apr 15, 2022 · An effective and complete processing route for the recycling of sintered Nd-Fe-B scrap magnets was proposed. Sintered Nd-Fe-B magnets were subjected to the Hydrogen Decrepitation (HD) process at various temperatures in the range of 50–300 °C, at two different pressures, 50 kPa and 200 kPa, followed by vacuum dehydrogenation in the range of 720–820 °C. A study of the processing and characterisation of sintered NdFeB magnets made from recycled feed stock was undertaken. Initially the hydrogen decrepitated (HD) powder was investigated using two different milling techniques ball milling and burr milling. The powders were analysed with optical microscopy, with the aid of a magnetic field.May 5, 2017 · The room temperature hydrogenation causes decrepitation of the material, where the Nd-rich material forms NdH 2.7 and the Nd 2 Fe 14 B matrix grains form an interstitial hydrogen solution. The material expands by ∼5% and because of its brittle nature and differential expansion, undergoes decrepitation [16]. NdFeB-based alloys and magnets also react readily with hydrogen, and this has been exploited by the hydrogen decrepitation (HD) process [4]. During HD the material is exposed to hydrogen (at room temperature) and initially the Nd-rich phase absorbs hydrogen (represented approximately by Eq.Hydrogen Decrepitation and Recycling of NdFeB-type Sintered Magnets. Miha Zakotnik, E. Devlin, +1 author. A. Williams. Published 2006. Materials Science, Engineering. Journal of Iron and Steel Research International. View via Publisher. Save to Library.
Apr 15, 2022 · An effective and complete processing route for the recycling of sintered Nd-Fe-B scrap magnets was proposed. Sintered Nd-Fe-B magnets were subjected to the Hydrogen Decrepitation (HD) process at various temperatures in the range of 50–300 °C, at two different pressures, 50 kPa and 200 kPa, followed by vacuum dehydrogenation in the range of 720–820 °C. The oxidation kinetics in air of a commercial NdFeB magnet have been investigated over the temperature range 335–500°C. The oxide microstructure has been characterized by SEM, XRD and cross-sectional TEM. The results show that the external scale formed consists of an outer layer of Fe2O3 and an inner layer of Fe3O4 but that the principal degradation …The fabrication of Nd-Fe-B sintered magnets is composed of quite a few processes mainly including strip casting, hydrogen decrepitation, jet-milling, magnetic alignment and pressing, sintering and subsequent heat treatment, machining, and surface coating. ... Possible methods of recycling NdFeB-type sintered magnets using the …Absorption and desorption of hydrogen by the permanent magnet material Nd 2 Fe 1 4 B have been studied using a microcomputer‐controlled, thermomanometric analyzer with an initial hydrogen pressure of approximately 1 bar. Primary absorption occurs in the range 200–300 °C and results in the formation of a stable hydride with …Abstract. This paper reports the desorption of hydrogen from NdFeB powder, and unmilled material, produced using hydrogen decrepitation as a pre-milling technique, investigated using a mass spectrometer to monitor the hydrogen partial pressure in the system as the sample was heated under vacuum from room temperature to …The decrepitation process and related changes in the sample temperature are analysed to explain the experimentally observed weight gain curve of a Nd–Fe–B sample due to hydrogen uptake. It is shown that the expansion of the specific surface resulting from decrepitation of the sample is the most important parameter controlling …
Jan 1, 2007 · The rapid cooling of the strip flakes suppresses the growth of soft α-Fe branch crystal grains. The thickness of the strip flakes was about 0.25–0.35 mm. Hydrogen decrepitation (HD), which uses the expansion of hydrogen to break up the flakes, was followed by milling in a jet mill (JM). The particles were then accelerated to supersonic ...
Hydrogen processing of magnetic scrap (HPMS) as one of the best approaches for magnet-to-magnet recycling is thoroughly reviewed in this study in terms …A combination of hydrogen decrepitation (HD) and jet milling (JM) has been used to produce powder for the processing of permanent magnets. The procedure has proved to be very successful for both Nd-Fe-B (Neomax) alloys and the ND-Dy-Fe-Nb-B high coercivity alloys. The magnets produced by the HD/JM process showed excellent coercivities when …Oct 1, 2015 · Hydrogen is already used to process cast NdFeB in the Hydrogen Decrepitation (HD) process. The HD process is used extensively to reduce bulk (or strip) cast NdFeB ingots to friable, hydrogenated NdFeB granules/powder, prior to the production of jet milled powder which is then aligned, compressed and sintered to form fully dense sintered magnets ... Sep 14, 2000 · This way of powdering known as hydrogen decrepitation (HD) is a well-established stage of manufacturing technologies of sintered [2], [3] and bonded [4] Nd–Fe–B magnets. The interstitial hydrogen in the ferromagnetic Nd 2 Fe 14 B phase reduces significantly its anisotropy field H A. That is why desorption of hydrogen is necessary in order ... Hydrogen decrepitation (HD) is an effective and environmentally friendly technique for recycling of neodymium-iron-boron (NdFeB) magnets. During the HD process, the …
Hydrogen decrepitation (HD) is an effective and environmentally friendly technique for recycling of neodymium-iron-boron (NdFeB) magnets. During the HD process, the …
The influence of the alloy granulation grade, temperature and surface oxidation on the kinetics and the course of the fracture processes during the hydrogenation of Nd16−xDyxFe76B8 (x=0–3) alloy was studied. The average particle sizes of the alloy were 1 mm, 5 mm and 3 cm and the temperature range between 20 and 200 °C. Pre-oxidation …
The application of hydrogen decrepitation (HD) as a process for recycling Nd-Fe-B sintered magnets was reported in [ 6 ], in which the essential role of hydrogen in the recycling process was demonstrated. The obtained magnetic properties of the recycled magnet were ( BH) max = 290 kJ/m 3 (±5 kJ/m 3 ), Br = 1240 mT (±50 mT) and jHc = …An effective and complete processing route for the recycling of sintered Nd-Fe-B scrap magnets was proposed. Sintered Nd-Fe-B magnets were subjected to the Hydrogen Decrepitation (HD) process at various temperatures in the range of 50–300 °C, at two different pressures, 50 kPa and 200 kPa, followed by vacuum dehydrogenation in …Hydrogen decrepitation (HD) is based on the selective synthesis of neodymium hydrides though the reaction of hydrogen gas with neodymium located in the Nd-Fe-B magnet. HD process was originally designed and patented by Harris et al. (1979) as a way to break down SmCo and Sm 2(Co,Fe,Cu,Zr) alloys. 5 17. These magnets were identical in every way apart from the orientation of the Nd 2 Fe 14 B grains. Each magnet was exposed to hydrogen and the decrepitation behaviour observed. The anisotropic samples were found to decrepitate exclusively from the ends of the rods whereas the isotropic magnets were attacked by the hydrogen at all …The behavior of hydrogen absorption in the NdFeB Hydrogen Decrepitation process is affected by the shape of the NdFeB alloy, pressure and temperature curves of the reaction process, which makes the reaction process with characteristics of nonlinear, time-varying parameters and coupling. In this study, we proposed a state space modeling …Hydrogen decrepitation (HD)/hydrogenation disproportionation desorption recombination (HDDR) is a process used in manufacturing REPM and carried out as pretreatment before green body sintering. During hydrogenation, the Nd-rich grain boundary phase in NdFeB magnets initially absorbs hydrogen forming Nd hydride: [ 49 ].May 5, 2023 · The first is the hydrogen decrepitation (HD) process, which is already used in the primary production of NdFeB magnets to convert the alloy into powder form before further comminution. 46 The second process, named HDDR, which consists of two different steps, namely hydrogenation–disproportionation (HD) and desorption–recombination (DR), was ... calcium [12] and hydrogen decrepitation [1,13-19]. Many of these are under current development. Hydrogen decrepitation (HD) is based on the selective synthesis of …Abstract. Some fully dense, sintered NdFeB-type magnets (employed in VCM disc drives) have been subjected to a recycling process using the hydrogen decrepitation (HD) process. After a brief milling treatment, the powder was aligned, pressed and re-sintered and this procedure was repeated four times with a progressive fall in the density …Feb 1, 1997 · Hydrogen decrepitation of Nd-Fe-B type magnet alloys is a two stage process. Firstly, the hydrogen reacts with the Nd-rich phase at or close to room temperature. This is an exothermic reaction [4] and the heat evolved then allows the second stage to proceed in which the hydrogen is absorbed by the Nd^FeuB matrix phase.
Fig. 1. Illustration of the Hydrogen Decrepitation Press-Less Process (HD-PLP) recycling of anisotropic sintered NdFeB magnet. Passivated commercial N48M sintered magnets were used as starting material and hydrogen was applied to disintegrate the magnets inside a ball milling container. The hydride powder was both used directly …Jul 1, 2002 · The effective diffusivity of hydrogen in NdFeB magnets is reduced with Co and Ga additions and as a result of the texture induced in the microstructure via die-upsetting process. In addition to the results shown in Fig. 8 , the thermal desorption behaviour related to the hydrogenation of a die-upset MQU-G magnet is different for the two ... The processing and characterisation of recycled NdFeB-type sintered magnets. M. Degri. Materials Science, Engineering. 2014. A study of the processing and characterisation of sintered NdFeB magnets made from recycled feed stock was undertaken. Initially the hydrogen decrepitated (HD) powder was investigated using two…. Expand. The obtained strips were pulverized and further milled into ∼5 μm powder using hydrogen decrepitation and jet milling, respectively. These powders were pressed in a magnetic field of 1.8 T under a pressure of 8.0 MPa. Afterward, the green compacts were sintered at 1070°C for 3 h in vacuum, cooled by Ar quenching. ... NdFeB sintered …Instagram:https://instagram. 20 off dollar20ncaa manual 2022 23titanium x 24221career macy Permanent magnets produce magnetic fields and maintain the field even in the presence of an opposing magnetic field. They are widely used in electric machines, electronics, and medical devices. Part I reviews the conventional manufacturing processes for commercial magnets, including Nd-Fe-B, Sm-Co, alnico, and ferrite in cast and …Anisotropic powder was prepared with precursor (NdDy)-(FeCoNbCu)-B sintered magnets by hydrogen decrepitation, desorption, and subsequent annealing treatment. The hydrogen desorption was performed in magnetic fields of 0, 1, 3, and 5 T. The orientation of tetragonal phase grains of the powder was evaluated from the … gina holtmannnow gg A study of the processing and characterisation of sintered NdFeB magnets made from recycled feed stock was undertaken. Initially the hydrogen decrepitated (HD) powder was investigated using two different milling techniques ball milling and burr milling. The powders were analysed with optical microscopy, with the aid of a magnetic field. whatsapp image 2020 03 18 at 11.19.57.jpeg Novel hydrogen decrepitation behaviors of (La, Ce)-Fe-B strips. Jiaying Jin G. Bai +4 authors M. Yan. ... Doping with Dy/Tb is a current solution to improve the coercivity and the operating temperature of NdFeB magnets, by increasing the magnetocrystalline anisotropy of the (Nd, Dy/Tb)2Fe14B (2:14:1) …Hydrogen decrepitation process has been applied for the first time for the direct recycling of SmCo 5 magnets. Industrially produced sintered SmCo ... Nowadays, NdFeB magnets represent more than 90% of the REE permanent magnets production. But, SmCo magnets have much higher coercivity and better temperature resistance, and many experts expect ...